Design-build solutions for successful warehouse construction
As the nation’s largest builder of warehouse and distribution space, ARCO National Construction is an unrivaled warehouse contractor. The expertise of our staff, unmatched industry experience, and ability to provide the best overall solutions are what make us a leading warehouse construction company and trusted partner on projects coast to coast.
1000
Warehouse Projects Designed & Built
300
Million Square Feet of Warehouse Projects Completed
Expertise from a leading warehouse contractor
Backed by decades of experience and hundreds of warehouse projects completed, ARCO National Construction’s unparalleled industry expertise has established us as a trusted warehouse builder for clients nationwide. Our experience spans all project types including new builds, expansions, renovations, and tenant improvements. From large national developers and Fortune 500 companies to family-owned businesses, we take pride in being a valued partner in warehouse construction, regardless of project complexity or scale.
From speculative developments to large-scale distribution facilities for e-commerce end-users, CPGs, and 3PL providers, ARCO has the experience and expertise needed to help developers and owners achieve a successful warehouse development, regardless of complexity or scale.
- Speculative Warehouse Development
- Build-to-Suit Distribution
- 3PL
- New Builds
- Expansions
- Renovations
Featured Warehouse Projects
GET IN TOUCH.
Ready to kick off your warehouse project? We're here to connect and help you get started smoothly.
Tilt-Up Construction Compared to Pre-Engineered Metal Buildings
While initial construction costs for tilt-up buildings may be higher compared to pre-engineered metal buildings, long-term operational costs should be considered in addition to initial capital investment. Energy, maintenance, and alterations can all have significant cost impacts; tilt-up construction provides significant long-term cost savings in these categories, which can help offset the initial upfront investment.
”In a complicated construction and development environment, we feel confident in putting Scannell's reputation on the shoulders of ARCO. Over the course of our partnership, we have developed more than $350 million with the ARCO team and will continue to partner with them on future projects.
Courtney LehmanScannell Properties
Warehouse Design & Construction Considerations
When it comes to warehouse construction, there are many design and construction details that must be considered to achieve a successful development. Floor systems, exterior wall types, structure, bay sizing, building systems, and site design are all elements that should be explored in the earliest stages of a project to ensure the most functional and cost-effective facility.
Space utilization, pre-existing site conditions, schedule needs, and more can all play a role in determining the most advantageous option for each of these elements. Partnering with an experienced contractor that is actively engaged throughout the design and beginning stages of a project will ensure that the very best design and construction decisions are made, resulting in a superior finished product and the very best customer experience.
WAREHOUSE DESIGN & CONSTRUCTION
Floor Systems
Choosing the proper floor system for a warehouse requires the knowledge of concrete types, site dynamics, and how a space will be utilized. Concrete floors can be reinforced or un-reinforced, formulated to be freezer/cooler compatible, shrinkage compensating, and specific to the floor loading and equipment path needs of the user. The needs of the user should be established in the earliest stages of the project to determine the most advantageous floor system choice.
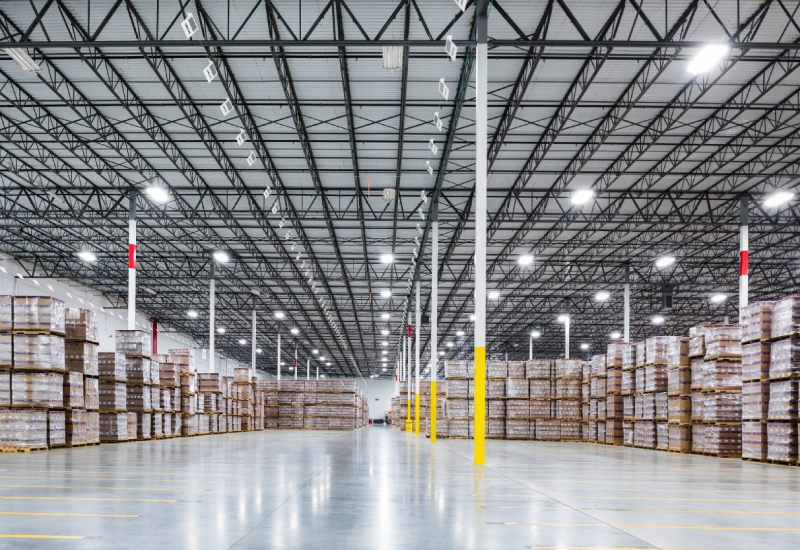
Traditional concrete
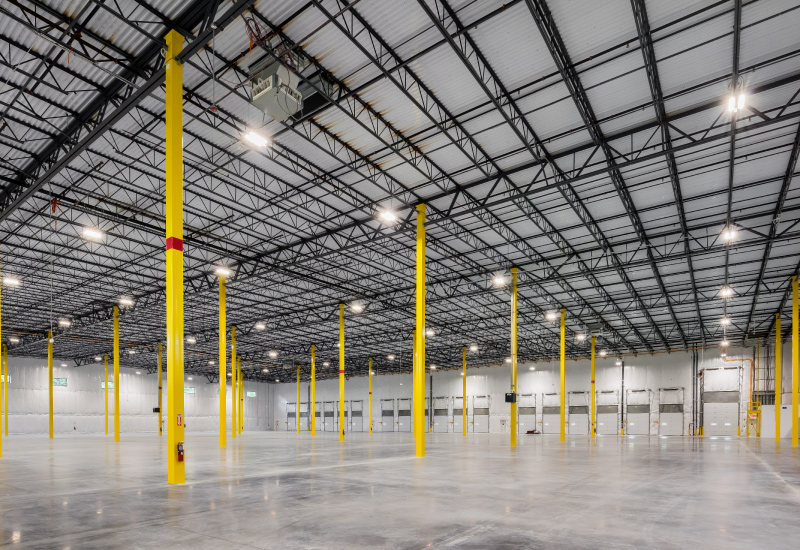
Ductilcrete
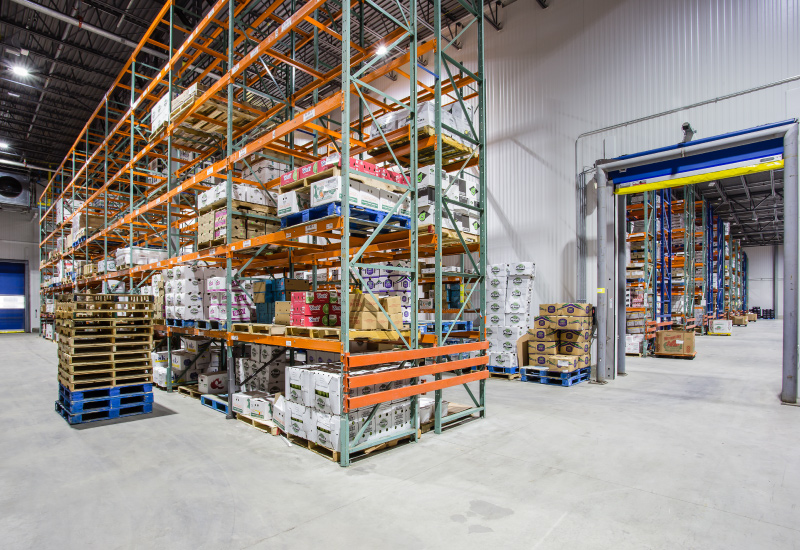
Shrinkage compensating
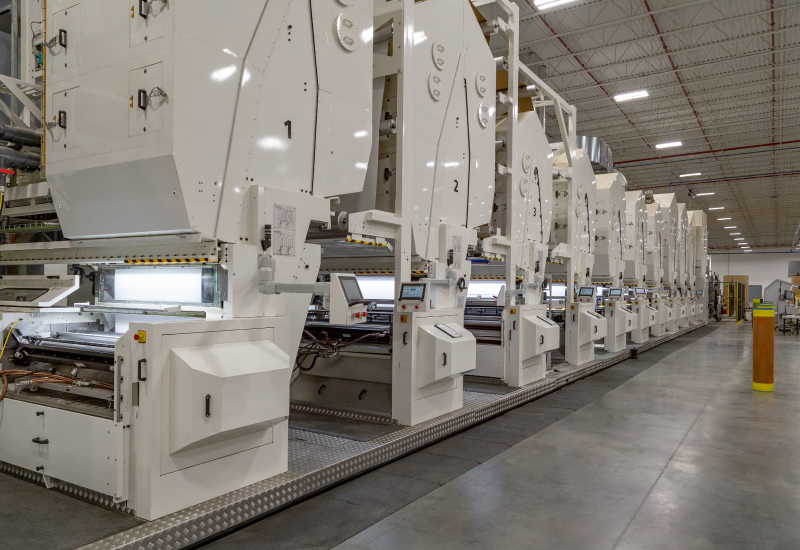
Heavy loaded floors/equipment foundations
WAREHOUSE DESIGN & CONSTRUCTION
Exterior Wall Types
Exterior wall type selection for warehouses is often based on building size, schedule needs, and exterior façade preferences. For larger warehouse facilities, uninsulated concrete panels poured onsite are typically the most cost-effective, and almost any exterior siding, cladding, or veneer can be applied to the outward facing portion. Precast panels are produced offsite year-round and installed prior to floor slab, making them the ideal choice in some circumstances in which schedule restraints are a concern.
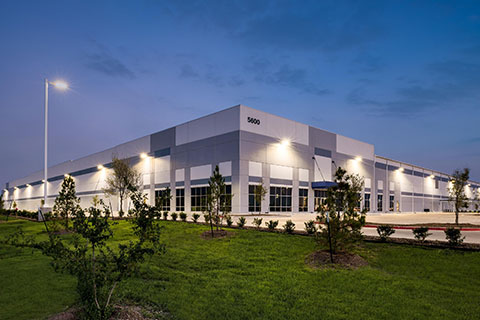
Concrete tilt-panel/non-insulated
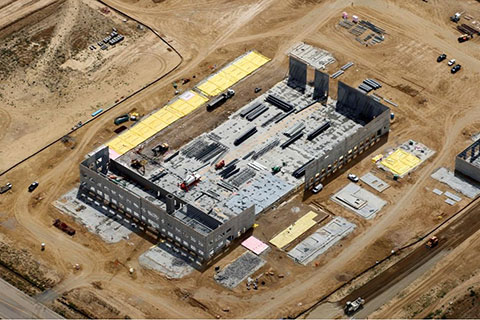
Concrete tilt-panel/insulated
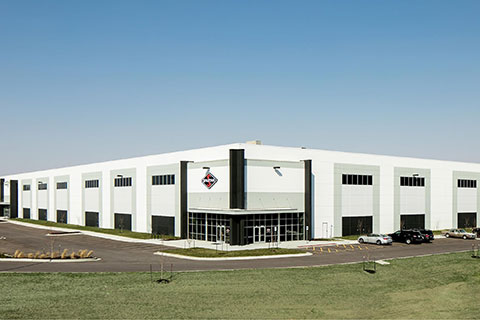
Precast tilt panels
WAREHOUSE DESIGN & CONSTRUCTION
Building Structure
When determining the structure of a warehouse facility, roof loads, wall cladding, and storage heights must be considered. Steel joists, girders, and column structures can be engineered to span almost any distance and designed to support significant roof loads. Pre-engineered metal buildings can accommodate almost any wall cladding including insulated metal panels, precast concrete panels, and block/masonry. For warehouses in which large storage heights are necessary, a rack supported structure may be the most appropriate. Rack supported structures maximize warehouse footprint space and are typically associated with AS/RS facilities.
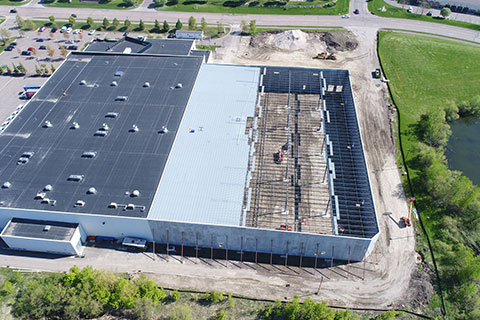
Steel joists
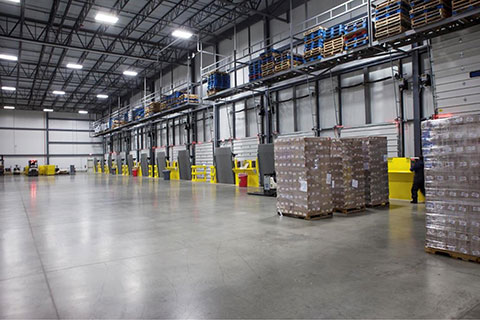
Pre-engineered metal building
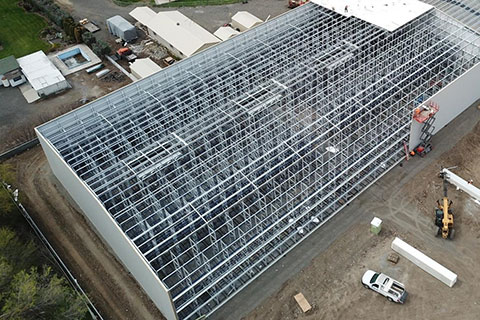
Rack supported
WAREHOUSE DESIGN & CONSTRUCTION
Bay Sizing
Bay sizing and racking layout options and standards are also important considerations in warehouse construction. Racking layouts, aisle sizes, and travel paths for forklifts are determined based on the width and clear height of the building. A warehouse contractor with the proper knowledge of industry standards regarding these factors is crucial to successful warehouse construction and the overall functionality of the facility.
ARCO’s site feasibility services empower clients to select the very best site for their facility. By providing site-specific cost information prior to construction, ARCO helps clients make decisions with full knowledge of their impact on cost and schedule.
WAREHOUSE DESIGN & CONSTRUCTION
Building Systems
Dock types, sizes, and specifications must also be determined in the design phase of a warehouse construction project. Owners can choose between mechanical and hydraulic docks based on their functionality needs. Additional building systems that must be considered include electrical service, HVAC, fire protection, and lighting. In addition to evaluating options and standards associated with these systems, it is also critical to understand code requirements to avoid design change orders and occupancy delays.
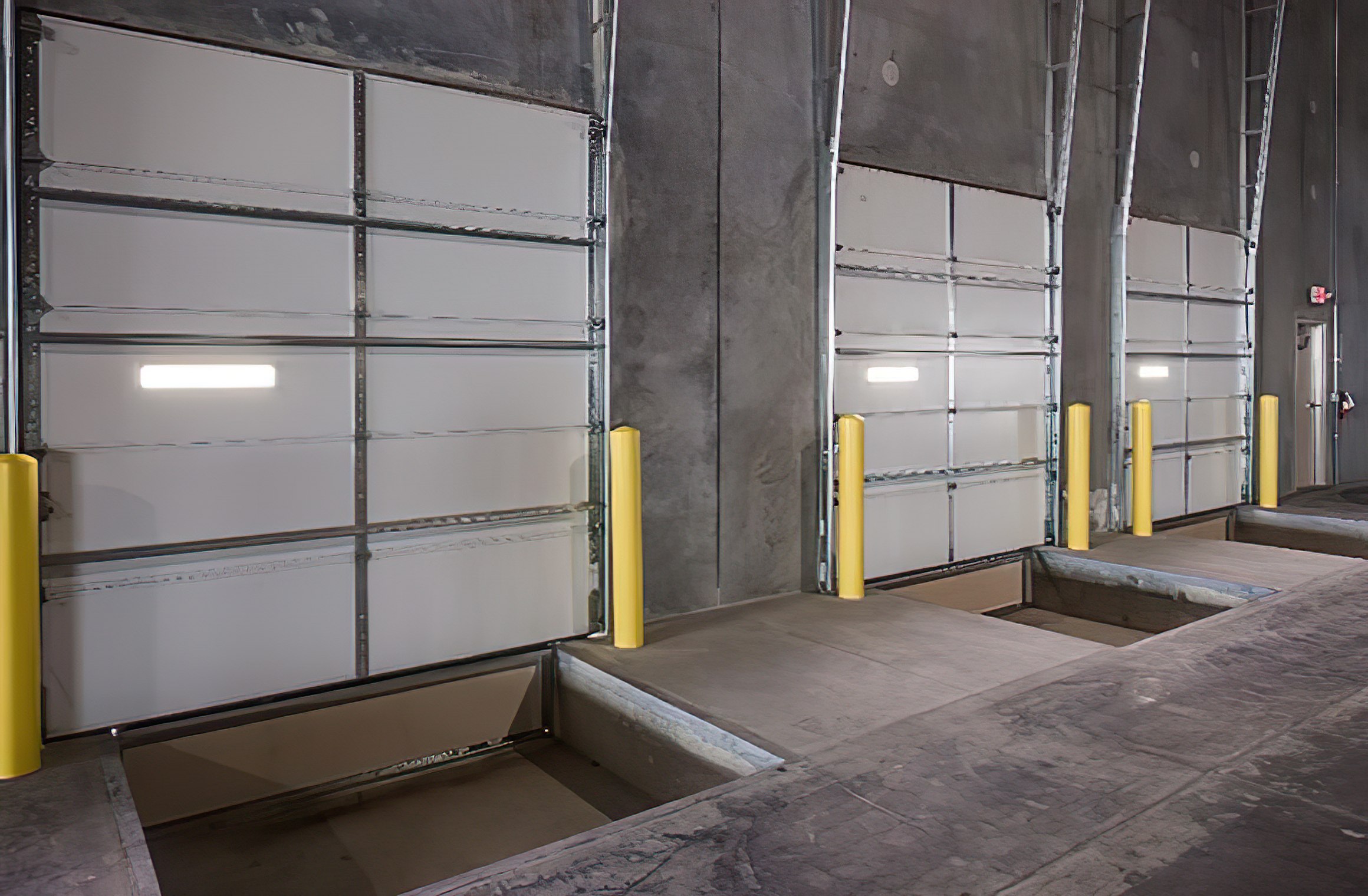
Mechanical docks

Hydraulic docks
WAREHOUSE DESIGN & CONSTRUCTION
Site Design & Selection
When it comes to site design, there are several rules of thumb regarding car parking per square foot, truck parking per square foot, docks per square foot, and office space per square foot. There are also standard dimensions for dock aprons, truck drive, truck parking, car parking, and drive aisles. Partnering with an experienced warehouse contractor will ensure that a warehouse facility’s site is designed to utilize the space in the most efficient and functional way possible.
Additionally, the increased competition for prime site locations has made challenging sites the new norm. ARCO’s site feasibility services empower clients to select the very best site for their facility. By providing site-specific cost information prior to construction, ARCO helps clients make decisions with full knowledge of their impact on cost and schedule.
WAREHOUSE DESIGN & CONSTRUCTION
Design-Build Delivery
Partnering with a qualified design-build contractor like ARCO with extensive experience in warehouse design and construction is essential for success. Design-build delivery helps clients navigate strategic design decisions and strategic planning for their facilities. Additionally, unlike traditional delivery methods that treat the phases of design and construction sequentially, the design-build process combines quality of design and construction, management of capital expense, and adherence to schedule all under a single point of responsibility. Preliminary design is completed during the proposal process, and warehouse users benefit now more than ever from the speed at which design-build delivery moves.
Contact Us