Manufacturing continues to drive demand for industrial space in markets nationwide as users look to improve their supply chains. The share of industrial requirements made up by manufacturers is around 18% – an over 350% growth since 2018 – and is expected to reach 25% by 2028. However, as demand for new manufacturing facilities rises, users are facing several key challenges, like intensified competition for suitable land, power resources, aging infrastructure, and the need for technological upgrades.
By partnering with a design-build contractor like ARCO National Construction, manufacturers can mitigate risks, reduce overall timelines, and ensure their projects are executed efficiently and successfully.
Competition for Land & Power Resources
For manufacturers, strategic site selection has become more critical than ever as speed to market has become a priority. However, site scarcity and utility infrastructure continue to pose significant challenges for new construction projects. With the increasing competition for prime locations, many manufacturers are finding it difficult to secure land that meets their operational needs. Additionally, power demands are high, with manufacturers competing against data centers and other energy-heavy industries for access to power-rich sites.
While it is impossible to eliminate these challenges entirely, partnering with a design-build contractor like ARCO can reduce timelines and ensure site feasibility. At ARCO, we perform thorough analysis of all site considerations to ensure a project is delivered with the best value. This includes evaluating key items such as site utilities and infrastructure, environmental conditions, geotechnical reporting, zoning requirements, stormwater management needs, and more.
As a design-builder, ARCO is involved in a project’s earliest stages, meaning coordination of key long-lead-time items, such as utilities, can begin as soon as possible. This early involvement significantly streamlines the process, helping reduce delays and ensuring that the facility is operational as quickly as possible.
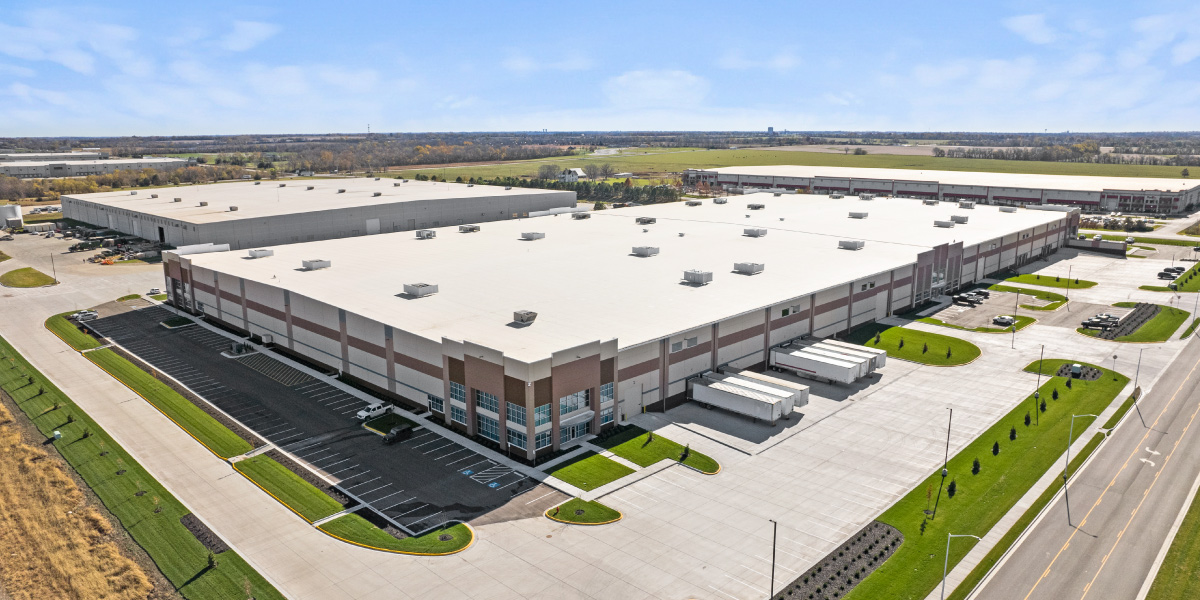
Aging Inventory & Advancing Technology
Aging existing assets and technology advancements are also key drivers for new manufacturing facility demand. In the U.S., approximately 52% of current manufacturing facilities are estimated to be between 30 and 60 years old. As technologies evolve, the need for modernized facilities that can support advanced manufacturing processes is becoming more apparent. Markets with older inventory, namely those of Detroit, Los Angeles, and New Jersey, will increasingly require updated facilities capable of integrating new technologies to enhance productivity, efficiency, and adaptability.
For manufacturers looking to upgrade their facilities, it is crucial to have flexible and adaptable designs that can accommodate future technology needs. ARCO works closely with clients to develop floor plans that can support current and future technologies and equipment requirements.
By designing facilities that are both flexible and forward-thinking, ARCO helps manufacturers remain competitive as the industry continues to evolve.
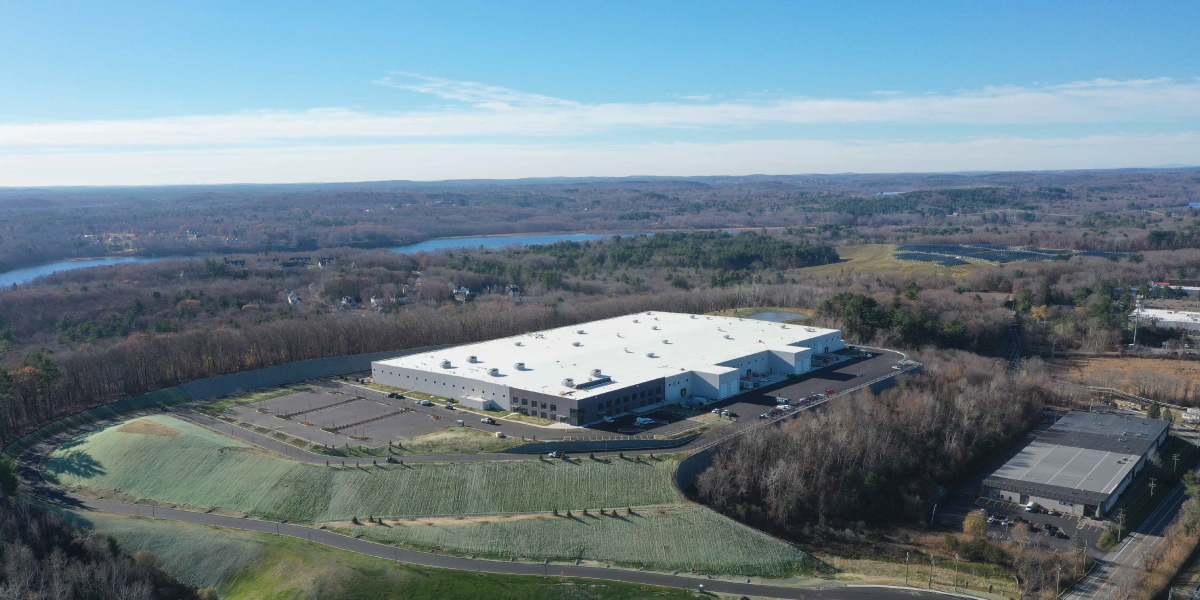
Strategic Facility Upgrades
In addition to building new facilities, many manufacturers are also opting to retrofit existing warehouse spaces, particularly if these locations offer desirable site benefits. Developers can position themselves to meet the demands of manufacturing users by proactively upgrading utility systems and incorporating features like reinforced floor slabs during the initial phases of construction.
These incremental upgrades can significantly improve speed to market, reducing tenant buildout times and making properties more attractive to manufacturing users who need to start operations quickly. Manufacturers can benefit from these improvements, as they won’t have to wait for costly and time-consuming upgrades to be completed.
ARCO can provide developers with expert guidance on key upgrades and the impacts from a cost and schedule standpoint, as well as help manufacturing users assess the feasibility of retrofitting existing spaces.
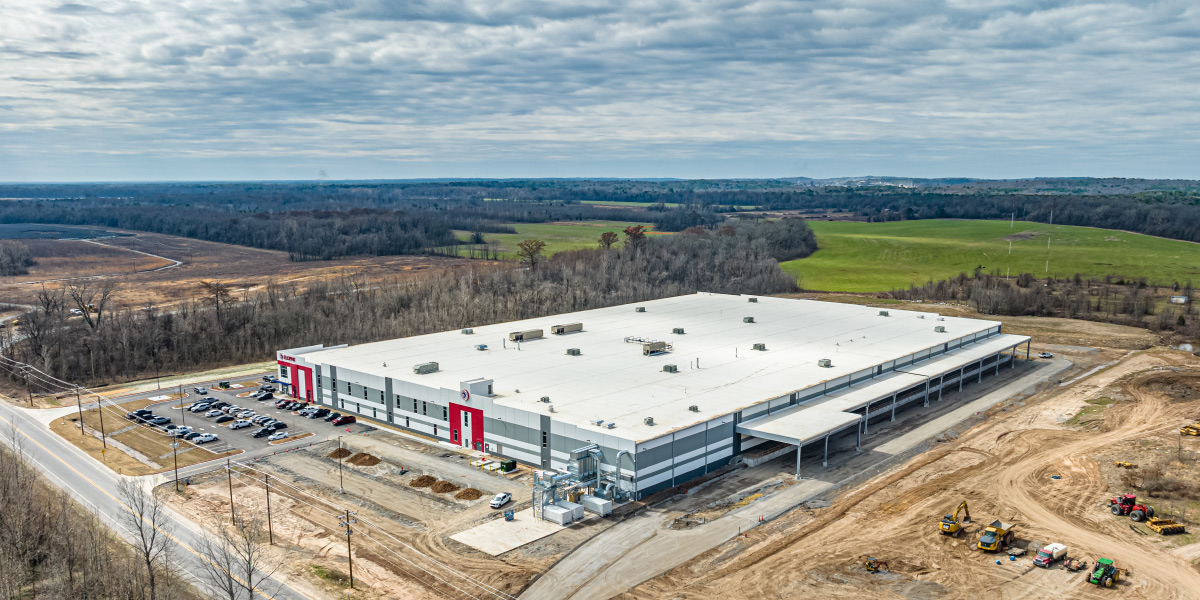
Addressing Market Challenges
While the challenges manufacturers face in today’s market can not be completely mitigated, partnering with an experienced design-build contractor like ARCO provides advantages compared to contractors who take a traditional approach.
ARCO’s design-build delivery helps clients navigate strategic design and planning decisions for their facilities. Additionally, unlike traditional delivery methods that treat the phases of design and construction sequentially, the design-build process combines quality of design and construction, management of capital expense, and adherence to schedule all under a single point of responsibility. Preliminary design is completed during the proposal process, and manufacturing users benefit now more than ever from the speed at which design-build delivery moves.
ABOUT ARCO NATIONAL CONSTRUCTION
ARCO National Construction is a premier, full-service design-build general contractor with more than 30 years of experience providing clients with complete project delivery throughout the United States. As the nation’s largest builder of warehouse and distribution space, we pride ourselves in offering the best, most cost-effective, single-source, turnkey solutions and adding value to every project.
With 48 offices in major markets coast to coast, ARCO offers the strength and presence of a national general contractor with the focus, attention, and regional expertise of a local builder. ARCO’s proven design-build approach combines quality of design and construction, management of expense, and adherence to schedule into a single point of responsibility. ARCO offers preliminary design at no cost to our customers to remove the risk of substantial upfront costs.